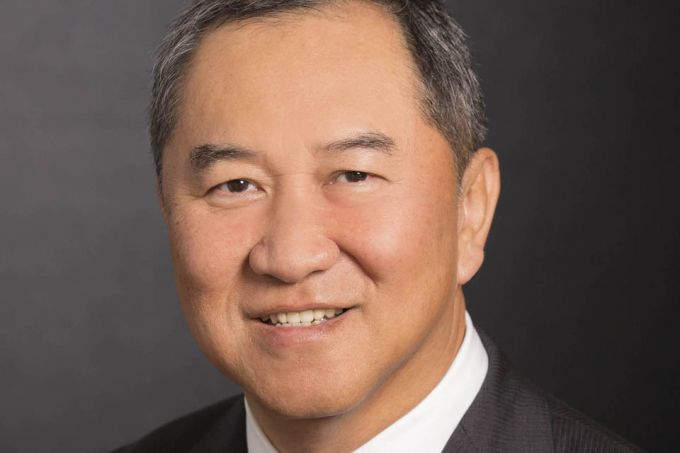
THE Singapore unit of Globalfoundries has won the Best Practices in energy efficiency award this year at the EENP Awards for a project that involves switching from hot to cold water for post chemical de-ionised (DI) water rinse, which is a low carbon innovative process.
In the wafer fabrication process, chemicals were used extensively to clean wafers. Traditionally, hot DI water generated by diesel fired boilers was used to rinse off the chemicals. This resulted in high diesel consumption.
To reduce diesel consumption, Globalfoundries explored the use of cold DI water for rinsing. Through rigorous engineering evaluation, chemical rinsing with cold DI water proved to be equally effective and efficient without affecting the functionality and reliability of the end-products. Hence, the company implemented the process change to switch from using hot DI water to cold DI water.
And instead of the large centralised boilers, localised optimum size boilers were placed near the manufacturing equipment to produce DI water for critical process tools.
This resulted in the saving of energy as well as the consumption of 6,821 litres of diesel fired per day. An annual energy reduction of 24,897 MWh was achieved which led to an annual carbon emission reduction of 6,875 tonnes CO2 equivalent.
As a result of these efforts, the company was able to decommission the diesel fired boilers in December last year.
Says K C Ang, senior vice president & general manager of Globalfoundries Singapore Pte Ltd (GFS): “GFS is very pleased to once again be recognised with the Award as the company completed another impressive energy efficient project. The GFS team challenged the conventional manufacturing process method all these years and adopted a positive change and a shift in paradigm to invoke disruptive and innovative change.
“Improving energy efficiency is a win-win for the company and the environment. The firm saves on energy usage and remains cost competitive. Going green also helps develop an eco-friendly and a low carbon manufacturing economy.”
Manufacturing companies like GFS should always do their best to be cost competitive by reducing energy usage through energy efficient projects and to be good corporate citizens with social responsibilities to the environment and climate, says Mr Ang. This way, the country and companies can be competitive and can make the transition to a successful low carbon economy. All companies should share and benchmark best practices so as to implement projects with lesser risk.
At GFS a company-wide energy management policy committed to by the management team has been implemented to ensure that the company plays its responsible corporate citizen role in energy usage optimisation, to be cost-competitive and go green with regard to the environment.
To achieve this, GFS has put together a team with members from various cross functional departments to keep coming up with energy efficiency solutions and projects. Examples of such projects include the re-design of furnace combustion chambers into smaller ones so that lesser LPG is needed. Also, GFS had upgraded its old chillers for cleanrooms to new and improved ones to conserve more energy. Other projects such as using LED lights to conserve energy and more solar power and panels to generate alternative electricity supply have also been undertaken.
GFS is developing new in-house capability in energy efficiency. Under its company-wide energy management policy, all the staff including the in-house cross functional teams are encouraged to look out for and contribute new ideas on energy efficiency. A team of energy manager and specialised engineers has been recruited and trained in various aspects of energy efficient expertise and equipment.
Moving forward, Mr Ang says that GFS “will continue to encourage all our staff to be energy efficient and to be prepared to embrace positive changes and sometimes challenge the norm and the conventional methods”.
“We should overcome resistance to positive changes especially if the new ideas work and improve our energy efficiency efforts. We should also involve the right people for the project team who will carry out the proper feasibility study, project analysis, intensive discussion, plan and thorough checks before the actual implementation.”
Globalfoundries Singapore is one of the largest semiconductor manufacturing companies in Singapore in terms of revenue and staff, investing more than S$4 billion over the last seven years. The company expanded its investments in Singapore by S$4.3 billion over the 2010 to 2017 period through its 5×8 inch giga-wafer fab plants and 1×12 inch giga-wafer fab plant by upgrading to new manufacturing equipment, productivity equipment (including the autonomous mobile robots), and also the conversion of the Fab 6 from 200 mm (8 inch) to 300 mm (12 inch) plant in 2013. It now has the capacity to produce 93,000 units of 8 inch wafers per month and 70,000 units of 12 inch wafers per month in Singapore.
Along with its manufacturing investments, GFS says that it has also pumped money into the R&D semicon technology establishing advanced emerging memory Magnetic RAM, Power Management, High Voltage, Ultra-Low Voltage and Ultra Low Leakage devices, MEMS Sensors as well as RF products.
The company says that its annual export revenue is more than S$2 billion and it has a staff strength of 5,500 in Singapore.