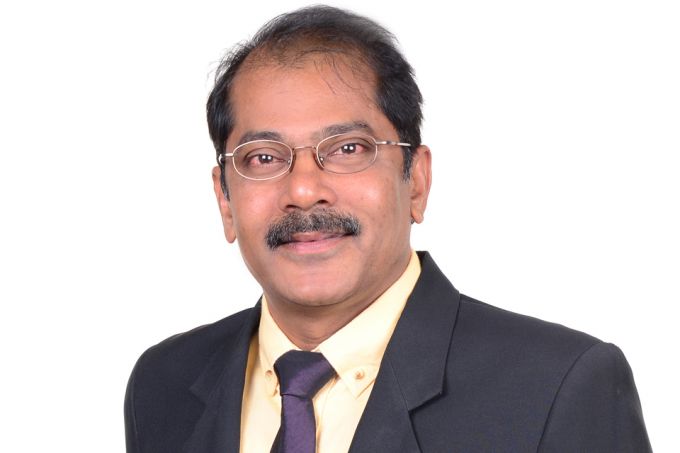
THE second Outstanding Energy Manager of the Year award winner Pandurangan Siva started his career in Asahi Kasei Plastics Singapore (APS) in 2007 as a senior engineer in the engineering department. His first project was to conduct a plant-wide energy audit with grant support from the National Environment Agency (NEA).
The following year he successfully implemented two of the recommendations – optimisation of cooling water pumping system and heat recovery from reactor outlet gas – and achieved significant annual energy savings of about 16 GWh. This motivated him to continue to drive energy efficiency (EE) within the company.
As production processes consumed more than 80 per cent of the facility’s total energy consumption, there was a need to raise awareness of EE among the production teams. Hence, in 2012, Mr Siva convinced the management to task the production teams with the energy management responsibility. He worked together with the production teams to set EE objectives and targets, provided training and ensured that they understood the objectives and improvements to be made before any project implementation.
Mr Siva, who is now energy manager at APS, is a Singapore certified energy manager. He has a Bachelor of Technology in Chemical Engineering and Master of Science in Safety Health & Environmental Technology.
“Energy cost for chemical industries is around 20 per cent of the operating cost. Most of these industries were set up 20 years back and use energy intensive processes and equipment in their operations. Through improving energy efficiency, industries can reduce their operating cost significantly. There are more perks of being energy efficient, it is not just operating cost. Industries can also reduce direct CO2 emission carbon tax, the price hike in raw materials, utility and other logistics services due to indirect CO2 tax,” Mr Siva highlights.
The current carbon tax for direct CO2 emission is S$5/ton. This tax is projected to grow more than three times higher in the near future, he says. By increasing energy efficiency now, industries can benefit through cumulative cost reduction over the life cycle.
Says Mr Siva: “Most of the corporates understand energy efficiency, but business competition, reduced margins and longer return on investment discourage them from taking immediate steps to implement EE. However, government agencies like EDB and NEA offer some attractive productivity improvement schemes to provide a helping hand to ease the corporate’s decision making.”
Singapore is an energy secured country in terms of uninterrupted power supply due to surplus electricity generation and regulation on production and distribution of the retailers by Energy Market Authority (EMA).
“The cost of energy utilities such as electricity and steam in the open market enhanced the business competitiveness among the suppliers. Consumers could choose the best supplier of the energy utility. However, no regulating authority controls their price, they only monitor and influence the cost of energy utilities,” says Mr Siva.
“In future, the energy utility retailers may pass down their direct CO2 emission tax to their consumers. If energy utility cost increases, consumers will increase their product cost to their downstream customers. It will be a cascading effect for Singapore chemical industries.”
Mr Siva says that his company is focused on its approach and emphasises energy efficiency in its operations. In 2005, APS implemented major modifications for heat integration to reduce steam consumption. The company installed three units of waste heat recovery boilers to produce low pressure steam. In 2008, it conducted a level three audit and identified many energy efficiency measures.
“After the initial success in energy saving in APS through a couple of applications, we brought about a huge cost saving for our operations and from then on energy efficiency has become a part and parcel of our operations,” says Mr Siva.
In recent years, APS has concentrated on process optimisation to reduce steam and water consumption. Every financial year, APS top management sets up objectives and targets to reduce consumption of steam and water for the production team. The production team will develop their management programmes to achieve the target. They closely monitor the effectiveness of the programme and update top management at the monthly meeting. At the end of the year, the result will be reviewed. Since 2014, APS has reduced its energy cost significantly.
As part of the plan for promoting energy efficiency, the company has decided to implement structured energy management system and conduct a level three energy audit. It is in constant search to implement new projects to reduce direct CO2 and emissions.
“APS is further developing an operation team to handle more energy efficiency project implementation. We also plan to provide training to other aspiring and potential engineers to become energy managers.”
Mr Siva says: “Being a chemical and process engineer, energy/electricity was not my area of specialisation. However, after starting to involve myself in the project and seeing the amount of wastage, it got me completely engrossed and every unit of energy saved gave me a sense of satisfaction. I did not realise it would lead me to this national level recognition. I am pleased to receive this prestigious award and this will motivate me further to look for other improvements in energy savings.”